AndrewBurns
Member
Nope these were exposed with my LCD screen contact printing setup, so true continuous tone and pretty well collimated light. You should probably ignore the aluminium plate I posted before because as I mentioned I used totally the wrong exposure times by accident (I used the inverse exposure times I was using when exposing my 6 test strips, rather than exposing each layer for the correct time during the stacking process).
That said, I did another test print with the 'correct' exposure times and the test pattern still came out far too dark, but this is probably because I really need to spend more time fine-tuning my exposure times for each layer so they get the correct amount of overlap rather than just trying to go straight to a final print.
Here's my second attempt at this print on aluminium. This time I put down a layer of liquitex matte acrylic varnish diluted 1+1 with water before coating with emulsion and that made a huge difference to how well the PVA adhered.
Previously I had to lay down very wet sloppy coats and if I tried to brush more than once the previous layers would start to tear off the aluminium, but using the varnish to improve adhesion gave me tons of time to even out the coats. I didn't do as good a job making even coats for the lighter layers which resulted in some pretty visible non-uniformity. You can also see some registration error here too, but I think that's easily solved.
What I am happy about here is how clean I managed to get the print to develop. Kees has mentioned a technique called 'spray development' on the Zerochrome page which amounts to just spraying water onto the print with a spray bottle during development. I've noticed that I keep having situations where the PVA melts but then stays on the surface even during violent agitaton, and I've had to use a soft brush to get it off, which always seems to leave some stain and risks damaging the image. This time I tried the spray development idea and it worked brilliantly. The spray bottle I was using seemed just perfect at jetting enough water onto the surface with enough force to push off the unexposed PVA without doing any damage to the exposed areas, I'll definitely try this method again.
I'm quite hopeful that with properly hardened gelatin sized paper and the spray developing technique I should be able to get good prints with minimal stain, even more-so with aluminium sheets which naturally resist staining. Now I need to go back and be a lot more methodical in working out the relative exposure times of my different layers so that they combine to make a tonal range much closer to linear than what I'm currently getting...
That said, I did another test print with the 'correct' exposure times and the test pattern still came out far too dark, but this is probably because I really need to spend more time fine-tuning my exposure times for each layer so they get the correct amount of overlap rather than just trying to go straight to a final print.
Here's my second attempt at this print on aluminium. This time I put down a layer of liquitex matte acrylic varnish diluted 1+1 with water before coating with emulsion and that made a huge difference to how well the PVA adhered.
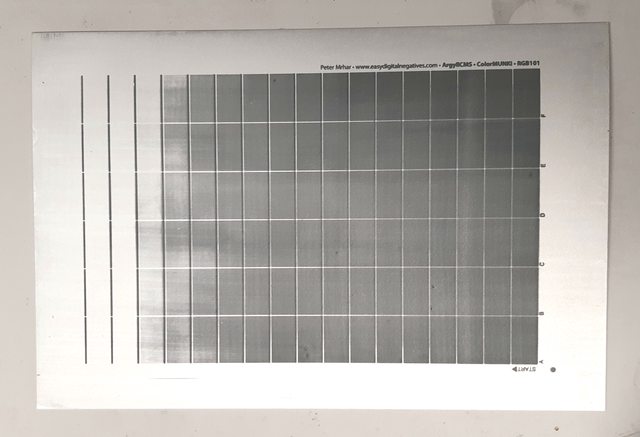
Previously I had to lay down very wet sloppy coats and if I tried to brush more than once the previous layers would start to tear off the aluminium, but using the varnish to improve adhesion gave me tons of time to even out the coats. I didn't do as good a job making even coats for the lighter layers which resulted in some pretty visible non-uniformity. You can also see some registration error here too, but I think that's easily solved.
What I am happy about here is how clean I managed to get the print to develop. Kees has mentioned a technique called 'spray development' on the Zerochrome page which amounts to just spraying water onto the print with a spray bottle during development. I've noticed that I keep having situations where the PVA melts but then stays on the surface even during violent agitaton, and I've had to use a soft brush to get it off, which always seems to leave some stain and risks damaging the image. This time I tried the spray development idea and it worked brilliantly. The spray bottle I was using seemed just perfect at jetting enough water onto the surface with enough force to push off the unexposed PVA without doing any damage to the exposed areas, I'll definitely try this method again.
I'm quite hopeful that with properly hardened gelatin sized paper and the spray developing technique I should be able to get good prints with minimal stain, even more-so with aluminium sheets which naturally resist staining. Now I need to go back and be a lot more methodical in working out the relative exposure times of my different layers so that they combine to make a tonal range much closer to linear than what I'm currently getting...