Niglyn
Member
Hi all,
I have come over from my thread
www.photrio.com
As it seems everybody has the same issue with sensors having width, thus as the ratio of curtain slit & sensor width reduces, measured exposure becomes under-read.
It seems the issue is well known & it is a case of living with it, there is no (easy) solution & providing the measured exposure is within ISO tolerance, that is good enough.
As ic-racer posted in the other thread, calibration is easily done with a known slot width, but as the two curtains are not indexed, again, we are back to the same issue.
Also, whilst a camera with flash sync at 1/30s would have a slot width of half at 1/60, quarter at 1/120 etc, a camera with different flash sync speed would have different slot widths for each 'speed' so one could not simply apply a correction based on measured exposure.
My thoughts are the following
a) it is a known issue with all testers, so accept the faster shutter 'speeds' will always read low, don't worry about it.
b) use the smallest hole possible to mask the sensor (we are now banging lasers at the sensor, so hole could be less than 0.5mm possibly.
c) use the curtain speed, which should not be affected by sensor width, to add a calibration value as the two sensors 'seen' time is used for this measurement, thus does not have the same measuring issue.
Is it just as simple as curtain travel speed over 32mm took 16mS.
so curtain travels 1mm (width of sensor) in 16/32 = 0.5mS
Apply the correction as follows:-
Laser blocked time = Laser blocked time - 0.5mS
Of course the shutter curtains will not run at a linear speed, so there will always be errors, but it might give a more accurate result?
Have I solved the Holly Grail?
I have come over from my thread
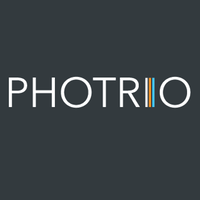
Build a shutter tester for Focal Plane shutters - Cheap, Easy & it Works
Right now I'm relying on the onboard VR. But I'm still a bit struggling on the best way to connect the battery. I have connected it to the GND and VIN port so to use the onboard VR, but I'm using 3 AA batteries, which results in 3x 1.5V = 4.5V. From what I understand, the input power on the VIN...

As it seems everybody has the same issue with sensors having width, thus as the ratio of curtain slit & sensor width reduces, measured exposure becomes under-read.
It seems the issue is well known & it is a case of living with it, there is no (easy) solution & providing the measured exposure is within ISO tolerance, that is good enough.
As ic-racer posted in the other thread, calibration is easily done with a known slot width, but as the two curtains are not indexed, again, we are back to the same issue.
Also, whilst a camera with flash sync at 1/30s would have a slot width of half at 1/60, quarter at 1/120 etc, a camera with different flash sync speed would have different slot widths for each 'speed' so one could not simply apply a correction based on measured exposure.
My thoughts are the following
a) it is a known issue with all testers, so accept the faster shutter 'speeds' will always read low, don't worry about it.
b) use the smallest hole possible to mask the sensor (we are now banging lasers at the sensor, so hole could be less than 0.5mm possibly.
c) use the curtain speed, which should not be affected by sensor width, to add a calibration value as the two sensors 'seen' time is used for this measurement, thus does not have the same measuring issue.
Is it just as simple as curtain travel speed over 32mm took 16mS.
so curtain travels 1mm (width of sensor) in 16/32 = 0.5mS
Apply the correction as follows:-
Laser blocked time = Laser blocked time - 0.5mS
Of course the shutter curtains will not run at a linear speed, so there will always be errors, but it might give a more accurate result?
Have I solved the Holly Grail?