kyuseok
Member
Hello, I've been using the first generation of Jobo CPE for about an year and suddenly it creates streaks along the perforations.
I already read this thread from Photrio already but since I do not do pre-rinse and I start rotating the tank right after I pour in the solution, it couldn't solve the puzzle unfortunately.
My JOBO rotates at constant, moderate speed at mode 1 and my go-to developer is Kodak D-76 stock. I thought it could be the fixer problem so I mixed a new batch of Ilford Rapid Fixer, didn't help as well.
The film was Fomapan 100 and I developed it for 5 minutes and 57 seconds at 20 degrees celcius.
What could be the cause of this calamity?
Any inputs will be appreciated! Have a nice day
I already read this thread from Photrio already but since I do not do pre-rinse and I start rotating the tank right after I pour in the solution, it couldn't solve the puzzle unfortunately.
My JOBO rotates at constant, moderate speed at mode 1 and my go-to developer is Kodak D-76 stock. I thought it could be the fixer problem so I mixed a new batch of Ilford Rapid Fixer, didn't help as well.
The film was Fomapan 100 and I developed it for 5 minutes and 57 seconds at 20 degrees celcius.
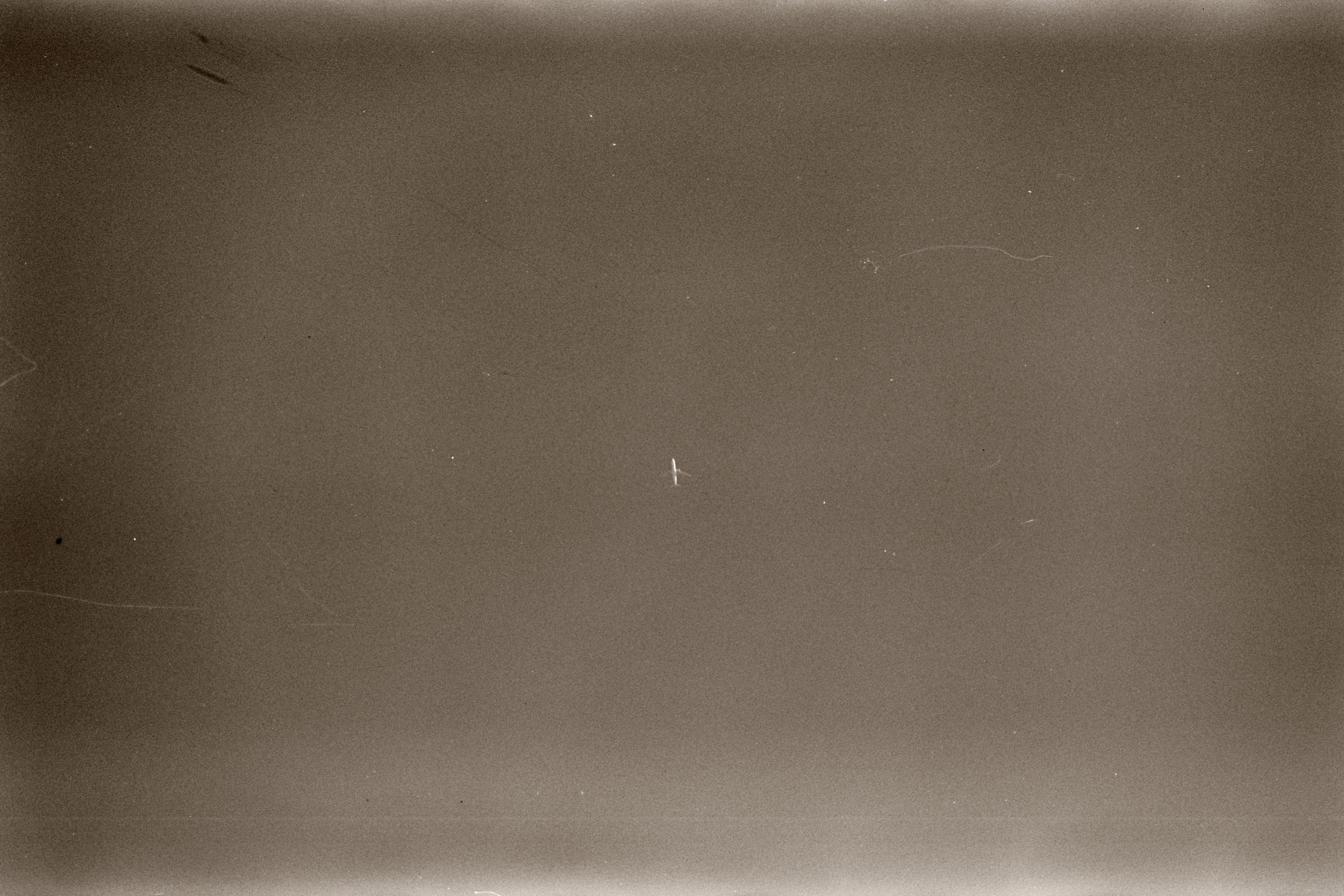
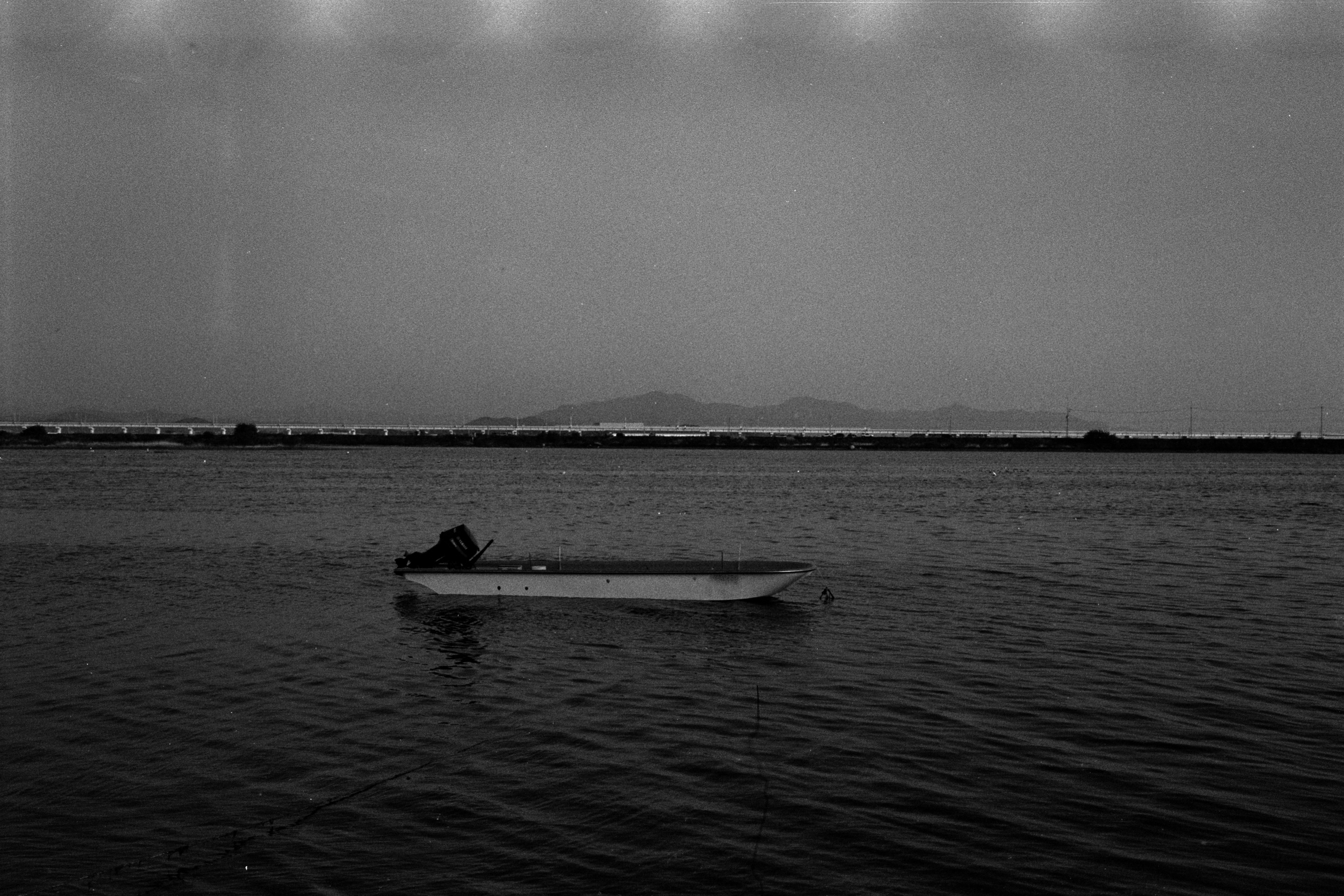
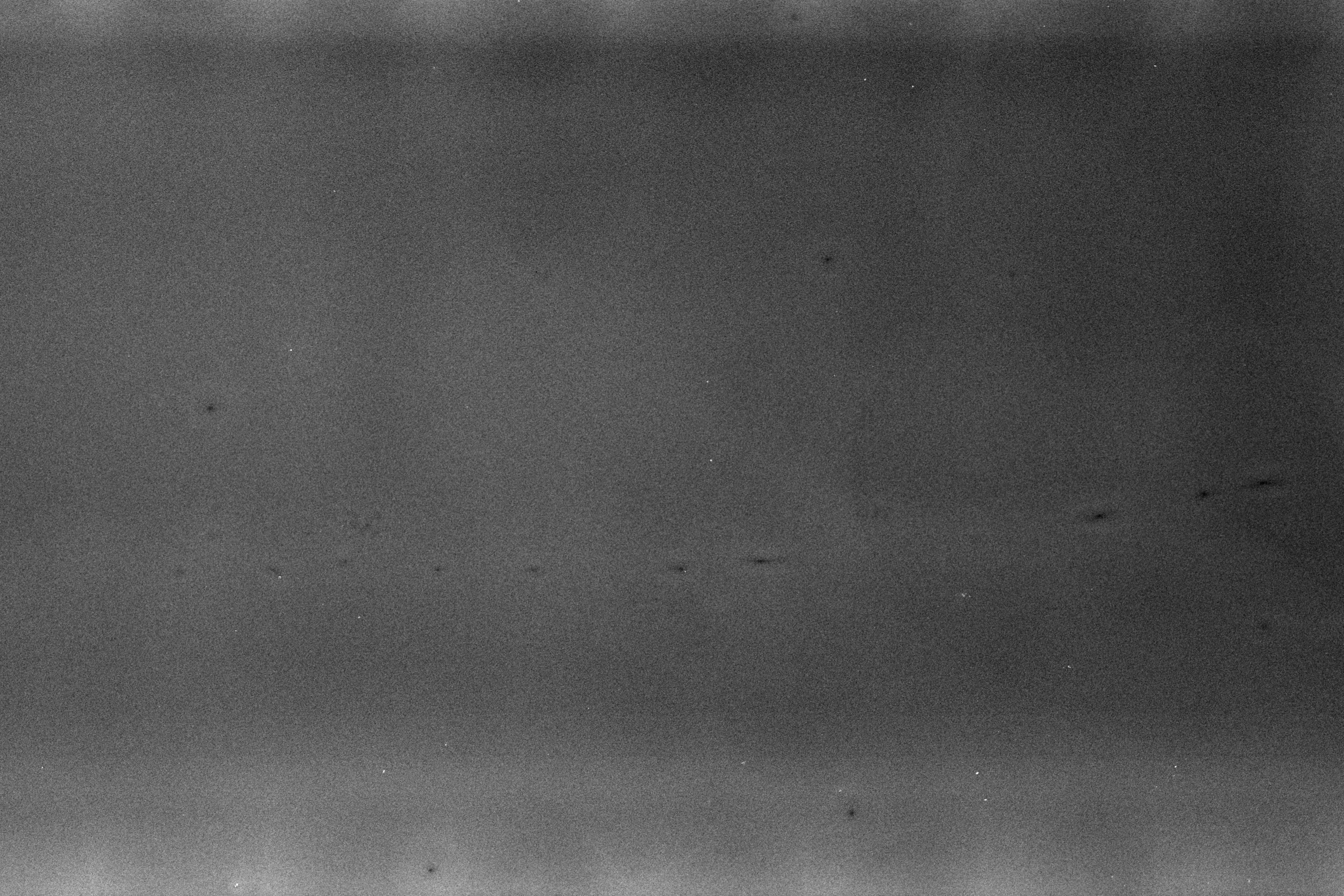
What could be the cause of this calamity?
Any inputs will be appreciated! Have a nice day
