Davec101
Member
Having extensively researched the idea of multi-layer platinum prints over the last few months I have finally had a chance to finish some tests and report on the results.
Multi-layered platinum printing was used with great success by the late Irving Penn who created some of the finest platinum prints in existence. This technique should not be confused with double coating, as with this method a print is coated and developed up to three times in succession with different negatives as opposed to coating…waiting..then adding a second coat and then exposing and developing..
I spoke to Richard Sullivan (of Bostick & Sullivan) a few weeks back on what his thoughts were on Penn’s technique using multiple layers of platinum sensitizers in succession and he was of the opinion that Penn was at the time using some quite difficult negatives to print in platinum (specifically colour ones) and thus required a separate number of inter-negatives to be created to achieve the desired result. However this does not take into account the high dmax that Penn’s print achieved ( I am hoping to get an exact reading of one of Penn’s prints in a week or so)
Richard some time ago came up with a similar method to Penn’s which I believe he used for multiple gum prints, however the bond Richard had identified to attach the printing paper to aluminium was reversible whereas Penn’s was not, this was key to me as I don’t wholly like the idea of platinum prints being attached by an adhesive whether it be acid free or not. Bonding the paper to aluminum also had the added benefit of making multiple registration relatively straight forward as the paper remains dimensionally stable.
Anyway enough of the back story, onto the results. I was initially sceptical that Arches Platine would accept 3 successive coats, so did not test or allow for a forth layer, however in hindsight I should of, if I get some time next week I will attempt this.
The pictures below are rather self explanatory, As stated the paper was Arches Platine which is bonded to aluminum, the sensitiser mix was the same for each coat, that being a mix of 1:3 in favour of palladium, exposure time was identical and the print was developed in Potassium Oxalate (70F).
For me personally this technique is a viable option for small prints aswell as larger prints in excess of 20x16 inches. I find with larger prints it is quite difficult to get a good first coat so another layer will always be beneficial. In terms of the final print results the multi-layered platinum prints I have created have a greater depth and richness to those that I have previously only single coated. It also opens up the possibilities of taking advantage of crafting individual negatives for each successive layer as well as mixing layers of just platinum or just palladium, something I have only really touched the surface of but intend to investigate this further over the coming months.
Multi-layered platinum printing was used with great success by the late Irving Penn who created some of the finest platinum prints in existence. This technique should not be confused with double coating, as with this method a print is coated and developed up to three times in succession with different negatives as opposed to coating…waiting..then adding a second coat and then exposing and developing..
I spoke to Richard Sullivan (of Bostick & Sullivan) a few weeks back on what his thoughts were on Penn’s technique using multiple layers of platinum sensitizers in succession and he was of the opinion that Penn was at the time using some quite difficult negatives to print in platinum (specifically colour ones) and thus required a separate number of inter-negatives to be created to achieve the desired result. However this does not take into account the high dmax that Penn’s print achieved ( I am hoping to get an exact reading of one of Penn’s prints in a week or so)
Richard some time ago came up with a similar method to Penn’s which I believe he used for multiple gum prints, however the bond Richard had identified to attach the printing paper to aluminium was reversible whereas Penn’s was not, this was key to me as I don’t wholly like the idea of platinum prints being attached by an adhesive whether it be acid free or not. Bonding the paper to aluminum also had the added benefit of making multiple registration relatively straight forward as the paper remains dimensionally stable.
Anyway enough of the back story, onto the results. I was initially sceptical that Arches Platine would accept 3 successive coats, so did not test or allow for a forth layer, however in hindsight I should of, if I get some time next week I will attempt this.
The pictures below are rather self explanatory, As stated the paper was Arches Platine which is bonded to aluminum, the sensitiser mix was the same for each coat, that being a mix of 1:3 in favour of palladium, exposure time was identical and the print was developed in Potassium Oxalate (70F).
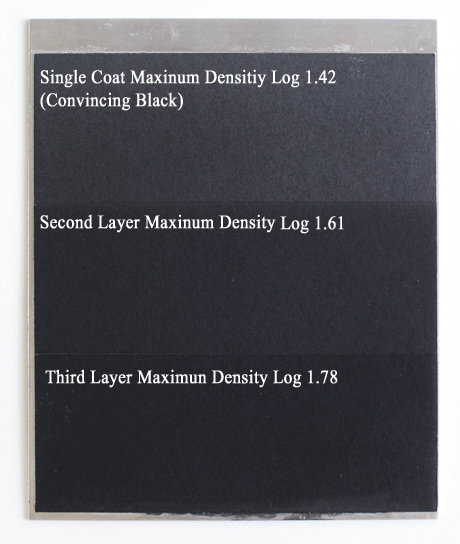
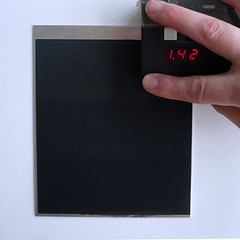
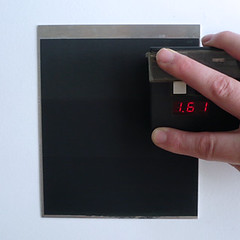
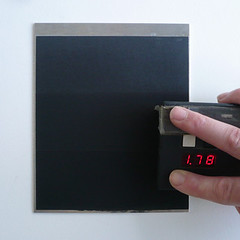
For me personally this technique is a viable option for small prints aswell as larger prints in excess of 20x16 inches. I find with larger prints it is quite difficult to get a good first coat so another layer will always be beneficial. In terms of the final print results the multi-layered platinum prints I have created have a greater depth and richness to those that I have previously only single coated. It also opens up the possibilities of taking advantage of crafting individual negatives for each successive layer as well as mixing layers of just platinum or just palladium, something I have only really touched the surface of but intend to investigate this further over the coming months.
Last edited by a moderator: